Every step of sapphire, jade and other stones, from mining, cutting, processing to polishing, is full of risks. From raw stone to finished product, it generally goes through processes such as material selection, cutting, design, rough carving, fine carving, and polishing. , among which, cutting is one of the initial processing of raw stones. Single wire cutting equipment is mainly used for square cutting processing of hard and brittle materials such as jade, jade and magnetic materials. The emery wire with diamond particles is reciprocated at high speed to achieve cutting of materials in the processing area, turning large materials into small pieces. materials to facilitate subsequent processing and production.
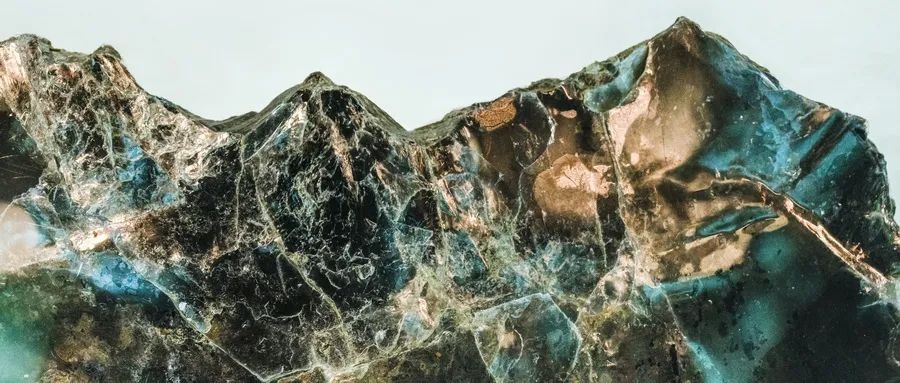
In order to meet the development needs of the industry, Sine Electric has launched a high-speed, stable, powerful and accurate jade single-line cutting equipment solution, which effectively improves the automation level of the jade cutting control system and promotes the iterative upgrade of the jade cutting process.
Solution Composition
Sine Electric’s jade single-wire cutting equipment solution uses Sine Electric’s EA300E series EtherCAT control solution, which consists of a motion controller, servo system, encoder, etc., which can accurately control the high-speed operation of the cutting equipment, making the cutting surface smooth and smooth while effectively shortening the cutting time. , to meet the needs of high speed, high precision and high efficiency.
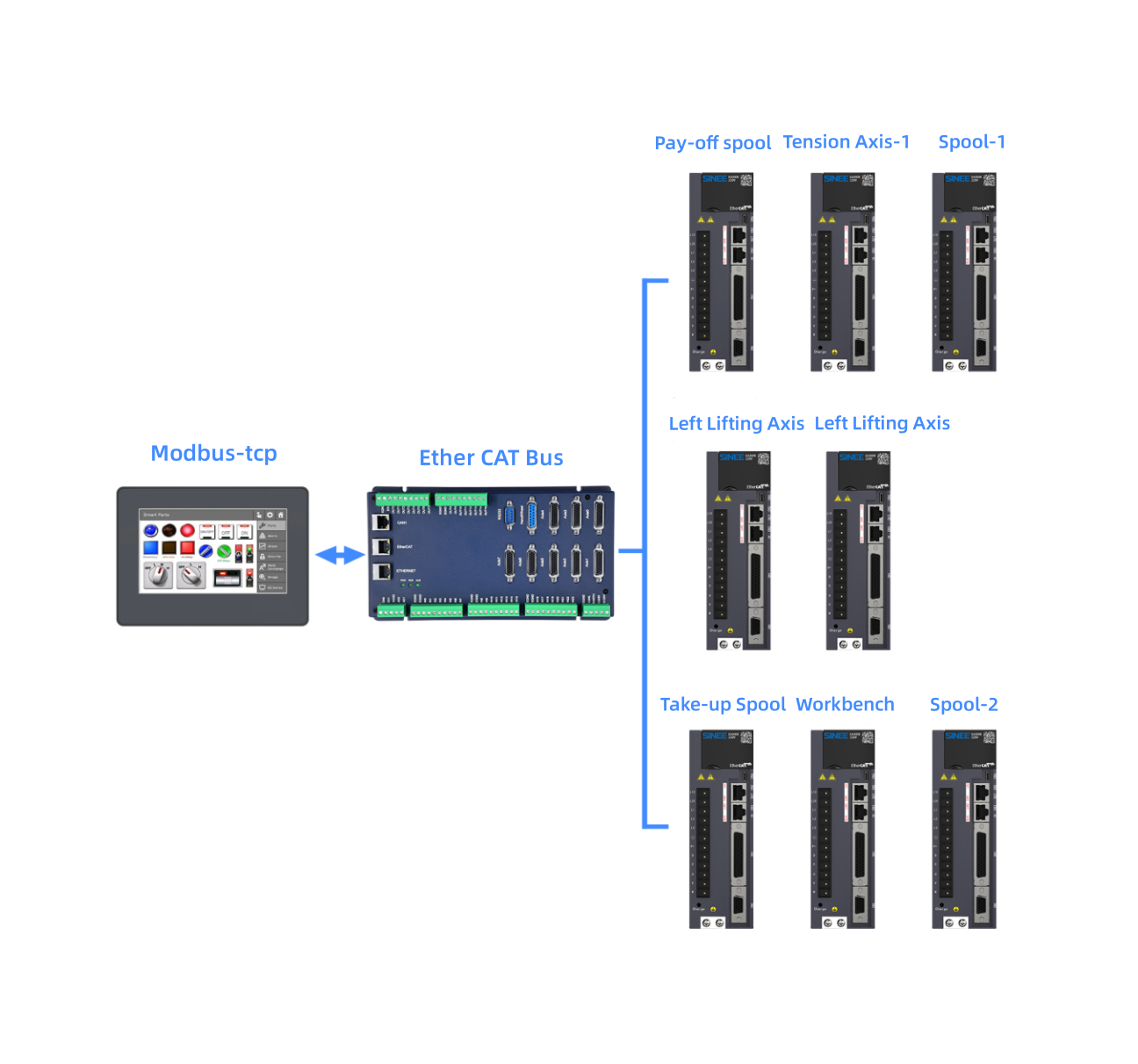
Controller: including HMI and motion control system, it is the core of the entire equipment and is mainly responsible for data calculation and processing, display of each status, and parameter setting;
Servo system: an important part of the entire solution. Responsible for executing electronic gear instructions and completing corresponding actions quickly and accurately, it has high requirements for responsiveness and stable performance.
Encoder: periodic calculation of retracting and releasing rod diameter.
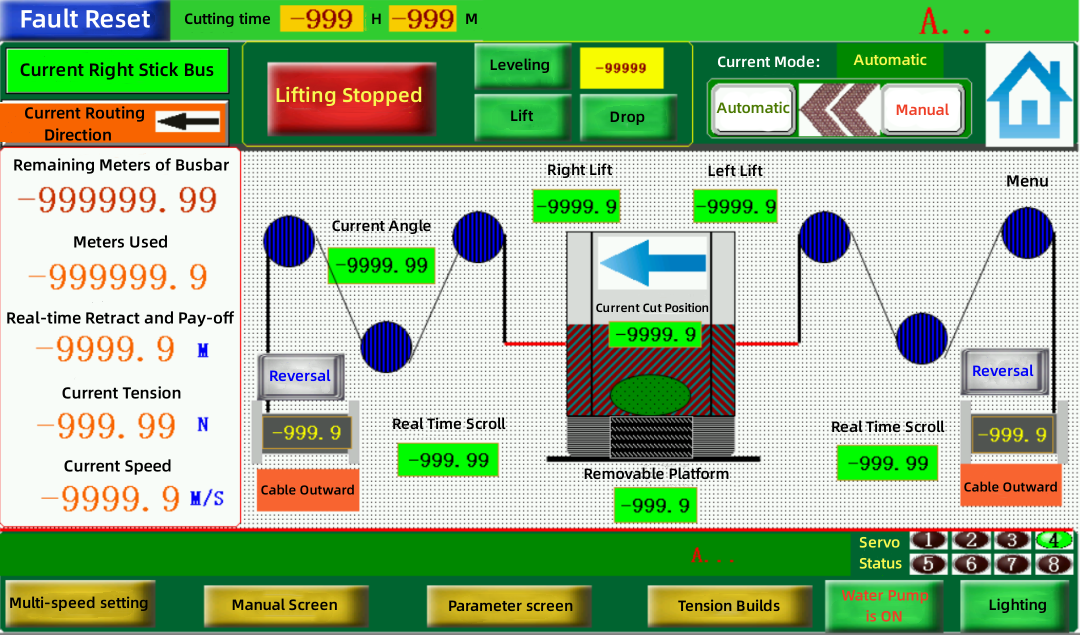
The efficient algorithm combines the cutting scene and cutting process to automatically and accurately calculate the running trajectory of each position to achieve fine process control.
Main Process
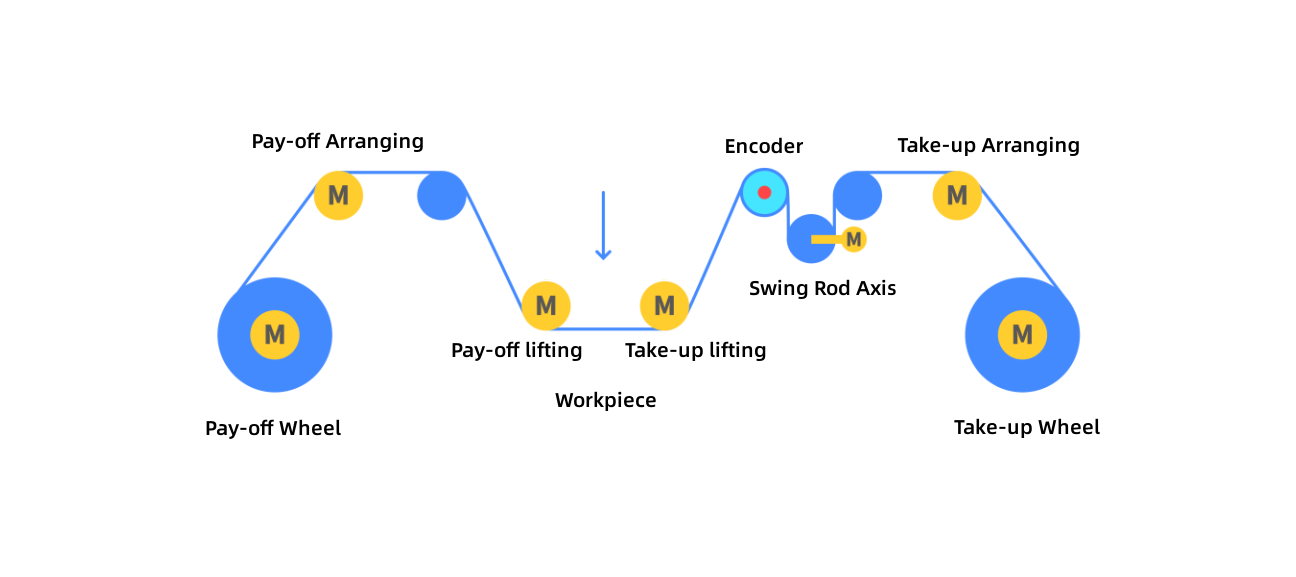
1. Using servo pay-off, the command speed of pay-off is obtained based on the automatically calculated pay-off coil diameter and the set cutting speed.
2. The two lifting servos are coupled to the virtual axis through gears, and the virtual axis moves downward by a feed speed, and then the up and down swing function is realized through superimposed instructions;
3. The swing rod shaft exerts constant tension on the line through torque control;
4. Using servo take-up, the command speed of take-up can be obtained based on the automatically calculated take-up diameter and PID.
Solution Advantages
>Double lift, smooth variable speed swing, keep the cutting surface smooth
>No need to heat the engine, you can start cutting at high speed after powering on
>No spindle tension control, saving electrical mechanism costs
>High-speed tension control, tension 15-60N, tension swing bar fluctuation ± 0.5
>PID parameter self-tuning
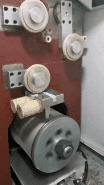
Application scenarios
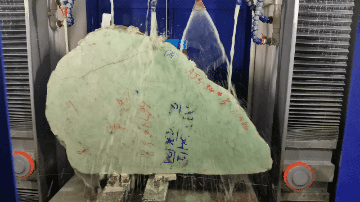
Sine Electric will continue to keep up with market demand, rely on automation platforms and in-depth understanding of industry processes, increase investment in research and development, provide more professional system solutions for various industries, and help customers achieve comprehensive improvements in production efficiency and corporate benefits.